信息中心
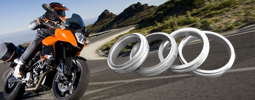
鼓式制動器、摩托車剎車圈、Drum brake、輪轂剎車圈專業生產廠家無錫九環2023年6月26日訊 早期汽車制動系統多采用鼓式制動器,隨著社會的不斷進步,汽車的車速越來越高、載重越來越大,人們對汽車制動系統的要求越來越高,盤式制動器憑借其整體結構緊湊、熱穩定性好和水穩定性好等優點逐步被人們所青睞。近年來越來越的汽車前后輪均采用盤式制動器,鼓式制動器漸漸退出汽車界。盤式制動器有著眾多優點,如以下所示:盤式制動器的整體結構較為緊湊,力的傳動效率高。同尺寸的盤式制動器與傳統鼓式制動器相比較,盤式制動器達到的制動效果更好。與鼓式制動器相比較,盤式制動器無自增力,因此其制動效果基本不受摩擦系數的影響。在熱膨脹方面,盤式制動器的制動盤徑向膨脹對制動效能無影響,而其軸向膨脹較小,因此盤式制動器在受熱膨脹后對制動效果影響很小。盤式制動器在制動時制動塊與制動盤之間單位壓力非常大,高速旋轉的制動盤存在很大的離心力,當盤式制動器涉水之后,在制動壓力和離心力的作用下,制動塊與制動盤之間的水很容易被擠出,因此涉水對其制動效果影響較小。盤式制動器的通常采用通風盤結構,通風盤散熱表面積較大,同時其安裝位置較為裸露,在車輪高速旋轉的同時加快了空氣流動速度,因此盤式制動器的散熱效果較好。在盤式制動器的結構上,制動盤與制動塊之間的間隔較小,從而大大減小了制動行程。同時與鼓式制動器相比,盤式制動器的熱膨脹較小,不會因熱膨脹帶來的行程增大問題,因此其反應更加靈敏。隨著制動次數的增加,制動盤與制動塊之間間隙會逐漸增大,而盤式制動器中的制動盤與制動塊之間的間隔可以實現自動調整。在維修方面,盤式制動器便于拆卸和裝配,損壞件一般為磨損量過大的制動塊,維修成本較低。按照制動壓力方式的不同盤式制動器可分為液壓式和氣壓式;按照固定制動塊結構的不同盤式制動器可分為全盤式和鉗盤式。全盤式制動器的制動背板和制動塊的形狀為圓環狀,在進行制動時制動盤的摩擦面與制動塊的摩擦面之間完全接觸。全盤式制動器的應用范圍較小,目前主要應用于少數重型汽車上,其可以作為制動器或緩速器。鉗盤式制動器的鉗體上有2~4 個制動塊,制動塊的摩擦面與制動盤的摩擦面之間接觸面積較小,其制動壓力較大,因此對制動塊材料的抗壓、耐磨能要求較高。以前人們將盤式制動器安裝在汽車上充當中央制動器使用,隨著盤式制動器的認可程度的提高,到現在已經成為各類汽車的標配。鉗盤式制動器分為兩種:定鉗盤式和浮鉗盤式。定鉗盤式制動器在汽車上的應用要早于浮鉗盤式制動器,定鉗盤式制動器的運動副較少,整體剛度較大,但因其制動盤兩側都設有活塞,布局困難,故而導致其尺寸較大。同時對油缸和活塞的精密度要求較高,導致了制造成本的加大。此外,因盤式制動器在制動時會使制動塊產生大量的熱,進而傳遞給制動液,導致制動液產生大量氣泡,最終影響制動效果。定鉗盤式制動器的鉗體是固定的,故而不作軸向移動。制動塊處于制動盤的兩側,當制動時鉗體內的活塞在油壓的作用下將制動塊推出,制動盤在兩側制動塊的擠壓下進行制動,如圖1.1 所示。浮鉗盤式制動器顧名思義其鉗體是不固定的,鉗體運動方式有兩種:沿導向銷做軸向平移和繞承銷擺動。因其油缸只存在于內側,故而使其結構簡單、易于布局,同時縮小了整體尺寸,較少了總質量,使得成本大大降低。浮鉗盤式制動器的內制動塊是可以隨活塞運動的,外制動塊是固定在鉗體上的。當汽車進行制動時,氣壓或者油壓會通過活塞將內制動塊推出,使其壓向制動盤,此時,鉗體會在反作用力下向制動盤一側移動,從而使兩側制動塊緊壓制動盤,最終達到制動的目的,如圖1.2 所示。以目前汽車上最為常見的浮鉗盤式制動器為研究對象,針對其工作時的受力狀況進行分析。首先對其工作原理進行分析:當汽車進行制動時,液壓(或氣壓)將內側鉗體中的活塞推出,帶動內制動塊向制動盤面接觸擠壓,鉗體橋在反作用力下會沿軸向向制動盤一側移動,從而帶動外制動塊接觸擠壓制動盤面,制動塊與制動盤相互接觸產生摩擦力,從而達到制動效果。當汽車停止制動時,液壓油流回油箱,制動壓力消失,同時在回位彈簧的作用使兩側制動塊恢復到原來位置,至此制動過程結束。在汽車的制動過程中,由司機踩下剎車到汽車速度降為零時,其過程大致可以分為三時期:第一時期為汽車的反應滯后時期。這段時間由于制動踏板會有運動行程和制動盤與制動塊之間存在間隙,從而導致此階段制動器沒有起到制動的作用。第二時期為盤汽車開始制動一直到車輪抱死時期。這段時間制動器的制動力矩不斷增大,汽車的車輪滾動與拖滑交替出現,最終使車輪抱死。第三時期為車輪抱死拖滑到汽車速度降為零時期。這段時間制動器的制動力矩基本保持穩定,最終汽車速度降為零。本文需要以最大制動力矩為標準,進而各部件在受到最大制動力矩后性能保持不變為前提進行研究設計。其簡化圖如圖1.3 所示。關于盤式制動器的仿真分析研究,國外研究文獻較多,但多數文獻局限于對盤式制動器的振動模態分析、制動噪聲分析和熱力學分析等方面,針對盤式制動器結構輕量化方面的研究較少。在彈性力學方面,17 世紀70 年代,R.HooKe 提出了胡克定律,指出固體材料的彈性變形與其所收到的外力是成正比的。19 世紀20 年代,A.L.Cauchy、J.C.B.Saint Venant 和C.L.M.H.Navier 等人創立了數學彈性理論。1871年,M.Levy 把塑性應變應力的研究有二維增加到三維[25]。在有限元分析軟件方面,1969 年,Pedro 公司發布了非線性有限元程序軟件MARC。1972 年,Hibbitt 創建了HKS,從而發布了ABAQUS 軟件。1989 年,美國Altair 發布了HyperMesh 軟件,在1994 年進一步研發出了OptiStruct 模塊。國外汽車輕量化設計最早應用在方程式賽車上,因為比賽會限制賽車的車身重量。1973 年,全球爆發石油危機,導致越來越大的汽車廠商開始注重節能技術,其中汽車車身輕量化設計屬于重要設計部分。汽車輕量化設計主要包括對其車身的輕量化設計和零部的件輕量化設計,在汽(1)采用鋁合金、鎂合金、復合材料和陶瓷等質量較輕,性能較好的材料為制造原料,在根源上減輕了零部件的質量。(2)通過運用計算機技術對汽車的結構進行模塊化設計,使得設計質量不斷提高,進而實現輕量化設計。在1994 年,國際鋼鐵協會成立了ULSAB 項目。ULSAB 項目運用的技術包括:另外,各國一些研究院所對汽車輕量化設計技術做了很多年的研究,并取得了豐富的成果。在歐美日國家,多數汽車生產商降低油耗的方法是降低汽車零部件的重量。通過CAD/CAE 軟件可以對汽車的零部件進行結構和尺寸的優化。現在,許多發達國家的汽車零部件生產商都擁有自己的CAD/CAE 系統。隨著我國汽車需求量的不斷提高,汽車的生產量也越來越大,進而帶動了盤式制動器產量的提高。我國盤式制動器的制造水平越來越高,較著名的生產廠商有重慶紅宇、亞太機電和萬向錢潮等。我國汽車起步較晚,在汽車零部件的制造方面落后更為嚴重。近幾年國內汽車產業發展迅速,汽車零部件輕量化材料的研發發展迅速。在汽車結構的設計方面,國內已經徹底擺脫了經驗設計,運用現代CAD/CAE 技術對汽車結構進行優化設計。在我國北京航空航天大學研發出了的CAD 系統CAXA,此模塊主要針對的是結構設計的輕量化技術,通過有限元法和優化設計方法進行結構優化,進而較少了零部件的質量。根據中國汽車工業協會統計,我國在2008 年汽車專用盤式制動器需求量達到了2755 萬臺,亞太機電已成為最大的盤式制動器制造商。與美、日、德、韓等汽車強國相比,我國在汽車輕量化方面的起步較晚,目前尚有許多共性關鍵技術問題亟待解決。幾年來,國內汽車零部件輕量化材料的研究和應用發展迅速,鋁合金、鎂合金、高性能鋼板在汽車上得到了廣泛的應用。如奇瑞汽車的艾瑞澤7 發動機采用了鋁合金材料;一汽和奇瑞轎車的部分車身采用高強度鋼。在汽車結構優化設計,中國已經完全擺脫過去主要依靠經驗設計,CAD/CAE 設計法分析靜態和動態強度的優化使用。在近幾年文獻中,米潔和吳欲龍采用多目標模擬退火法對盤式制動器進行優化設計,在保證盤式制動器可靠性的前提下減小其尺寸和摩擦副的升高溫度。王良模、彭育輝等人通過對盤式制動器的受力分析情況,建立了鉗體和托架的力學模型,利用CAD/CAE 軟件求建立有限元模型后進行靜力分析得出了鉗體和托架的在工作狀態下的應力及分布,表明了設計強度符合要求。王宏斌利用CAD/CAE 技術通過建立有限元模型對盤式制動器的結構進行了輕量化設計,經過優化后的盤式制動器總重量減輕了20.69%,減少了偏磨,在性能指標上均滿足盤式制動器的需求。
?